Automated Technology Courses
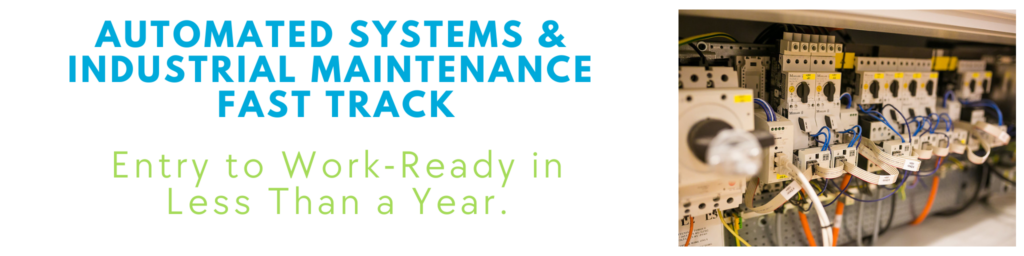
For individuals who want to start a career in industrial maintenance or automated systems, we offer a three-course series focused on either electrical or mechanical skills. Each class may be completed in about one month’s time and leads to certification from the Smart Automation Certification Alliance (SACA). Course descriptions are below.
Industrial Maintenance: Electrical Career Pathway
- Electrical I
- Programmable Control Systems
- Variable Frequency Drive
Skills Attainment (A la Carte)
Individuals with prior experience in industrial maintenance and automated systems who want to attain new skills may take individual classes (a la carte option) instead of enrolling in the three course series. Courses may be taken in any order and lead to stackable credentials that work together to build a training portfolio.
Course Descriptions
Electrical Systems I prepares individuals to connect, adjust, operate, troubleshoot, and analyze electrical circuits using basic electrical components: resistors, capacitors, inductors, DC motors, solenoids, manual switches, relays, fuses, circuit breakers, transformers, and indicators. Other key skills include: adhering to electrical safety rules, reading electrical circuit diagrams, applying Ohm’s Law and Kirchoff’s Law, using digital multimeters, interpreting series/parallel circuits, and assessing power/circuit protection.
Electrical Systems Installation I prepares individuals to install and test/commission electrical motor control circuits using these electrical components: control cabinet enclosures, 3-phase AC motors, reversing magnetic motor starters with overloads, control relays, timer relays, pushbutton switches, selector switches, limit switches, pressure switches, indicators, electro-pneumatic solenoid valves, safety disconnect switches, and circuit protection.
Electric Motor Control Systems I prepares individuals to connect, adjust, and operate electrical motor control circuits using these electrical components: 3-phase AC motors, reversing magnetic motor starters with overloads, drum switches, control relays, timer relays, pushbutton switches, selector switches, limit switches, pressure switches, and float switches. Other key skills include: adhering to motor control safety rules, reading ladder logic circuit diagrams, checking for proper ground connections, wiring motors for high and low voltage, and interpreting common motor control application circuits.
Motor Control Troubleshooting I prepares individuals to troubleshoot and remedy faults in electric motor control circuits and AC variable frequency drives. Skills include: adhering to troubleshooting safety rules, systems troubleshooting, component testing, and using digital multimeters, clamp-on ammeters, and PLC status indicators. Components include: AC VFD drives with volts per hertz capability, 3-phase AC motors, reversing magnetic motor starters with overloads, drum switches, control relays, timer relays, manual switches, limit switches, pressure switches, and float switches.
Programmable Controller Systems I prepares individuals to program, configuration, adjust, monitor, and operate industrial programmable logic controller (PLC) systems. Key skills include: adhering to PLC safety rules, performing normal startup/shutdown, operating PLC in different modes, performing emergency shutdown and reset, monitoring for proper operation through indicators and PC-based PLC software, configuring processor software drivers for communication to PC, configuring and loading of HMI programs, operating HMI with PLC, configuring PLC discrete I/O, transferring programs between PC and PLC processor, interpreting basic and intermediate level PLC ladder logic programs (with contacts, coils, timers, counters, math, comparison instructions), PLC project creation/editing, and interpreting common PLC program logic applications using electro-pneumatic actuators and on/off motor control systems.
Pneumatic Systems I prepares individuals to connect, adjust, operate, and analyze pneumatic circuits using these components: quick connect fittings, tee and cross fittings, air compressors, filters, regulators, lubricators, gauges, rotameters, directional control valves, flow control valves, check valves, cylinders, and motors. Other key skills include: adhering to pneumatic safety rules, reading pneumatic circuit symbols and diagrams, applying the Force-Pressure-Area formula, converting absolute/gauge pressure units, performing reciprocating compressor startup/shutdown, applying Pascal’s Law, setting pressure switch, filter draining, setting lubricator rate, lubricator refilling, and measuring delta P.
Mechanical Power Systems I prepares individuals to install, adjust, align, tension, operate and analyze basic mechanical power transmission drive systems using these components: motors, shafts, flexible jaw couplings, fractional horsepower (FHP) chain drives, FHP v-belt drives, spur gear drives, pillow block bearings, and flange bearings. Other key skills include: adhering to mechanical drive safety rules, mounting and leveling motors, testing and correcting for soft foot, installing components and shafts with keyways, sizing keys, aligning shafts using feeler gage and straight edge method, calculating speed and torque from component size ratios, interpreting rotary power specifications, determining mechanical efficiency, greasing bearings using a grease gun, refilling oil lubrication reservoirs, interpreting lubrication specifications, and identifying component given a model number.
Robot Systems Operations I prepares individuals to set up, adjust, monitor and operate industrial robot systems in an Industry 4.0 automation environment. Key skills include: adhering to robot safety rules, identifying robot types and robot components (and end-effectors), performing normal startup and shutdown, performing emergency shutdown and recovery, identifying robot work envelope, performing robot safety inspection, using teach pendant to view menus and status indicators, using teach pendant to jog robot in joint mode or using Cartesian coordinates, adjusting jog speed, setting and testing robot joint travel limits, using teach pendant to identify robot position in each of 5 frames, defining a frame using 3-point method, loading a robot program using Ethernet or memory card, testing digital robot inputs and outputs, testing robot program in single step or continuous mode, selecting and running robot program using teach pendant, teaching/adjusting robot points using proper frame, identifying/recovering from a fault, and viewing/interpreting robot alarm history.
Sensor Logic Systems I prepares individuals to connect, adjust, and operate discrete (on/off) electronic sensors and relay control sequence circuits using these components: inductive sensors, capacitive sensors, magnetic reed sensors, photoelectric sensors, hall effect sensors, limit switches, control relays, timer relays, manual switches, DC motors, indicators, electro-pneumatic solenoid directional control valves, and pneumatic actuators. Other key skills include: selecting sensor type for an application, reading ladder logic circuit diagrams, and interpreting common relay-control sequence applications circuits.
Variable Frequency Drive Systems I prepares individuals to connect, configure, adjust, and operate AC variable frequency motor drives using basic volts per hertz mode. Key skills include: adhering to VFD safety rules, operating VFD in manual using keypad, performing normal VFD startup and shutdown, performing emergency shutdown, viewing and editing parameters, changing speed with potentiometer, interfacing/configuring external discrete I/O, interpreting error codes, resetting drive errors, and configuring for acceleration, deceleration and braking.